Seleccionar el tamaño adecuado de la malla de una criba vibratoria es crucial para una separación eficiente del material, la productividad y la longevidad del equipo. Aquí tienes una guía paso a paso para ayudarte a tomar la decisión correcta:
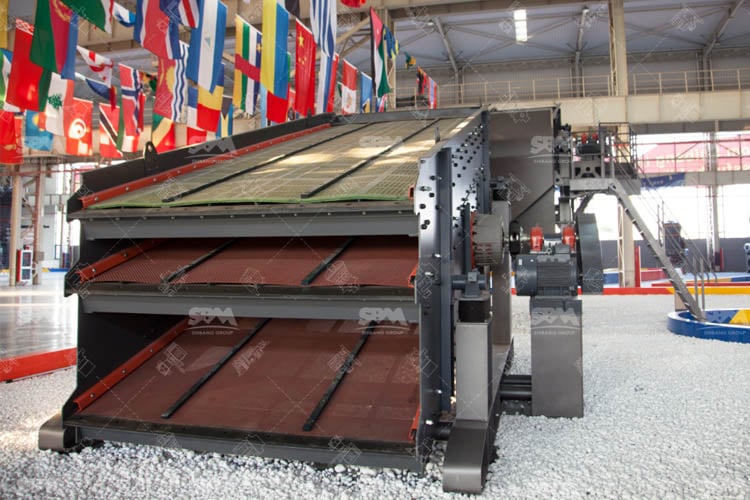
1. Determina las características de tu material
Distribución del tamaño de las partículas:
- Realiza un análisis de tamiz para identificar el rango de tamaño de tu material (por ejemplo, 0–5 mm, 5–10 mm).
- Elige un tamaño de malla que coincida con tu punto de corte deseado (por ejemplo, malla de 4 mm para separar agregados de 3–5 mm).
Tipo de material:
- Materiales abrasivos (por ejemplo, granito, basalto) → Usa malla de acero de alta resistencia para mayor durabilidad.
- Materiales pegajosos/arcillosos → Opta por mallas recubiertas de poliuretano o caucho para evitar obstrucciones.
- Materiales ligeros (por ejemplo, astillas de madera, pellets de plástico) → Considera aberturas más grandes para un mejor flujo.
2. Comprende los estándares de tamaño de malla
Número de malla (Tamaño de tamiz de EE. UU.):
- Se refiere al número de aberturas por pulgada lineal (por ejemplo, malla 10 = 10 aberturas por pulgada, ~2 mm de apertura).
- Un número de malla más alto = aberturas más pequeñas (cribado fino).
Tamaño de apertura (mm o micras):
- Mide directamente el espacio entre los alambres (por ejemplo, malla de 5 mm para agregados gruesos).
- Rangos comunes:
- Cribado grueso: 3 mm–100 mm (por ejemplo, piedras de cantera).
- Cribado medio: 0.5 mm–3 mm (por ejemplo, arena, grava).
- Cribado fino: <0.5 mm (por ejemplo, polvos, minerales).
3. Ajusta el tamaño de la malla a la eficiencia de cribado
Rendimiento vs. Precisión:
- Aberturas más grandes → Mayor capacidad pero menor precisión.
- Aberturas más pequeñas → Mejor precisión pero menor rendimiento.
Ejemplo:
- Para cribado de roca de cantera, usa una malla de 10–50 mm para un alto volumen de salida.
- Para clasificación de arena de sílice, una malla de 0.1–1 mm asegura una separación precisa de partículas.
4. Considera el porcentaje de área abierta
Definición: La proporción de espacio abierto respecto al área total de la malla (mayor = mejor flujo).
Regla general:
- Materiales gruesos: 50–70% de área abierta (por ejemplo, malla de alambre tejido).
- Materiales finos: 30–50% de área abierta (por ejemplo, malla de placa perforada).
5. Ten en cuenta la humedad y la pegajosidad del material
Materiales húmedos/pegajosos:
- Usa mallas autolimpiantes (por ejemplo, poliuretano con paneles tensados).
- Evita mallas muy finas (<1 mm) para prevenir obstrucciones.
Materiales secos:
- La malla de acero estándar o de acero inoxidable funciona bien.
6. Selecciona el material adecuado para la malla
Material |
Mejor para |
Vida útil |
Acero al carbono |
Cribado de propósito general, bajo costo |
Moderada |
Acero inoxidable |
Entornos corrosivos/húmedos |
Larga |
Poliuretano |
Materiales pegajosos, reducción de ruido |
Muy larga |
Caucho |
Impacto fuerte, resistencia a la abrasión |
Larga |
7. Prueba antes de la implementación a gran escala
- Pruebas de laboratorio/piloto: Realiza una prueba a pequeña escala para verificar el rendimiento de la malla.
- Ajustes: Si ocurre obstrucción, prueba con una apertura más grande o un diseño antiobstrucción (por ejemplo, aberturas cuadradas vs. ranuradas).
Errores comunes que debes evitar
- Ignorar la forma de las partículas: Materiales escamosos o alargados pueden necesitar mallas ranuradas.
- Pasar por alto la resistencia al desgaste: Materiales abrasivos requieren acero endurecido o poliuretano.
- Combinar mal la malla y la intensidad de la vibración: Las mallas finas necesitan vibraciones de mayor frecuencia.
- END -